
NewsInformation Center
Scratch and Abrasion Resistant UV Coatings:Various Approaches
2018/10/25
Abstract
UV-curable nanocomposite coatings of different appearances and properties were prepared and
evaluated. Selection of nanoparticles, oligomers, and monomers were made based on market demand of UV-curable urethane acrylate for adhesives and coatings. Targeted improvement areas included antiabrasiveness, tensile strength, hardness, optical clarity, and dimensional stability, while minimizing adhesion loss and elongation. Preparation method of nanoparticle/oligomer/monomer was chosen in consideration of cost effectiveness and, facility accessibility for manufacturing. Functionalized nanoparticles, multifunctional oligomers, and multifunctional monomers were used in developing appropriate products. A number of samples showed significant improvement of antiabrasion, dimension stability, and good adhesion.
Introduction Polyurethane acrylate oligomers can be polymerized under UV/EB radiation at room temperature in a short period of time. All components in a formulation can be made curable without giving out significant volatile organic components (VOC). Such formulations are plausible candidates for varnishes, adhesives, and coatings when fast curing, temperature sensitive application, and low VOC products are preferred, especially at the time when high output, low environment and regulatory burden,and outstanding performances are a market norm.
Stand-alone oligomeric systems have limitations in mechanical, optical, magnetic, electrical,
and/or biological performances, some of them critical for targeted applications. For example, some end users want products with high scratching and abrasion resistances, while others may want transparent products with longevity against weather. Efforts have been made through formulation and embracing new technologies for improvements. In recent years, significant scientific advancements have been made on nanotechnology, the potential of which for many industrial applications have been found in propositions while actual applications are slow due to cost ineffectiveness or facility limitations. In this study, suitability of routine industry instruments and daily QC instruments will be explored for nanoparticle/oligomer development. Different combination of oligomers, nanoparticles, and monomers will be investigated to generate products with noticeable abrasive resistance.
Materials and Methods
Surface modification procedure of particles: active silica based nanoparticle was modified with trimethoxysilane-methacrylate. Nanoparticles were then mixed with oligomers and monomers to obtain samples. Film or test samples were made by UV irradiation on blends following addition of UV initiators. Samples were cured multiple passes at 20 ft/min. In antiscratch test, #0000 steel wool under 8 Oz or 16 Oz hammer head was applied to rub the films being tested for multiple times. The depth of tracks and area of damaged area were then used to characterize the antiabrasion efficacy of samples.
Anti-abrasion test is carried out under Taber model 503 abraser using wheels H-22. Weight loss from 12 stages of 1000 cycle tests were used to rate abrasion resistance. Pick adhesion test was carried out using a utility spatula to pick at the coating. Coatings formed on different substrates with the adhesion samples of interest was picked, and both the degree of difficulty to remove the coating from the substrate and the size of removed coating were used as parameters for adhesion quality. A number between 0 and 5 was assigned to indicate the quality of adhesion, with higher number indicating better quality. Cross-hatch adhesion test was carried out by making a cross-hatch pattern using a Gardco 11 blade 1.5mm crosshatch cutter. After the tape has been applied and pulled off, the cut area is then inspected and rated for adhesion strength. Higher number indicated that more pieces were hatched off by the test, and therefore weaker adhesion. Hardness was tested using a Durometer (Pacific Transducer). Tensile strength and elongation were evaluated using TT-1000 (Chem. Inst.). FTIR (Perkin Elmer Spectrum 100), GPC (Polymer Laboratories PL-GPC-50), viscometer, and DMA (Universal V4.7A TA Instruments) was used to evaluate relevant properties of samples.
Results and Discussion
Nanoparticles, modified or nonmodified, may be able to drastically improve the performance for coating or adhesives.1,2,3,4 High functionality oligomers have been selected for its known abrasive resistance. To develop products suitable for market place, not only scientific feasibility should be checked out, technology readiness, such as manufacturing capability and capacity, and cost effectiveness also have to be considered. The design matrix is listed below:
Table 1. Samples investigated in this study.
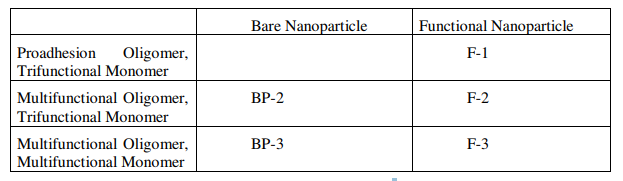
Dispersion efficacy for nanoparticle/oligomer/monomer blending was monitored by evaluating
homogeneity, transparency and viscosity before and after dispersion treatments. Transparency is one shortcoming for particle system. Two product series being investigated in this study, F-2 and F-3, showed no change in visible light absorption, making them eligible for optical applications. Figure 1 is an FTIR chart of F-2 before and after dispersion treatment. Big difference is observed at around the silica absorption peak of ~ 1100 cm-1 after each treatment, with the most noticeable differences observed after the first and the second treatments.
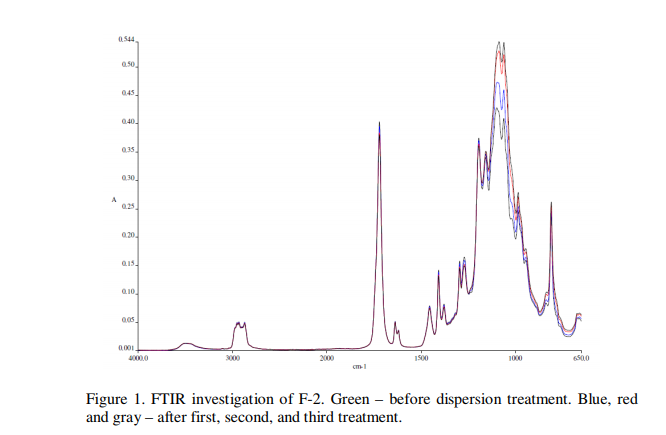
Viscosities also changed after each treatment. Table 2 listed viscosities of F-2 before and after treatments. The morphological change is also visually noticeable, with a more uniform blend obtained through dispersion. Some changed from hazy to transparent. It is believed that dispersion had helped the dissolution of nanoparticles to the oligomeric system, in part by breaking particle aggregates mechanically. Change of viscosities over time was also noticed.
Table 2. Viscosities of nanoparticle/oligomer system at different stages of treatments

DMA analysis of the nanoparticle/oligomer/monomer system was carried out (Figure 2). Over 2
degrees of increase in Tg was observed when 20% nanoparticle was added. To evaluate the change brought by nanoparticles, the apparent cross-linking densities, r, expressed in moles of elastically effective network chains per cubic centimeter of sample, were estimated from the Storage Moduli recorded at Tg+40 C using r = G’/RT = E’/3RT, where G’ is the shear storage modulus of the cured network at a temperature well above Tg, R is the gas constant and T is the absolute temperature at which the experimental modulus is determined. Cross-linking density with 20% nanoparticles was calculated to be 0.084 moles of elastically effective network chains per cubic centimeter of sample, significantly larger than that of 5% nanoparticles, 0.037 unit. The apparent cross-link density of control sample,which resembles uniformly crosslinked system, is also 0.037 unit.
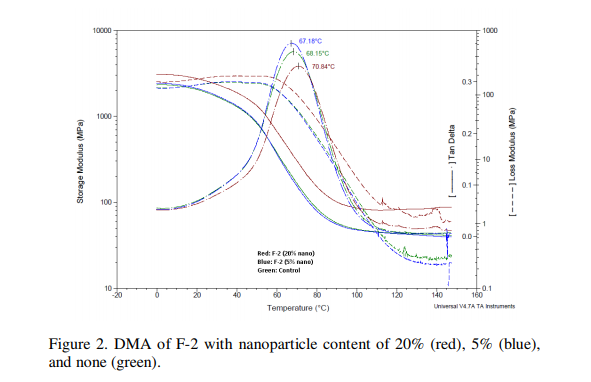
Antiscratch is often essential for coating applications, and was evaluated by steel wool test for samples under study. Most samples included in this report showed good antiscratch properties. Table 3 lists the test matrix and results for two samples. The nanoparticle enforced samples showed outstanding performance against samples without the particles, the control sample.
Table 3. Antiscratch test matrix using #0000 stool wool and test results samples F-2 and BP-2
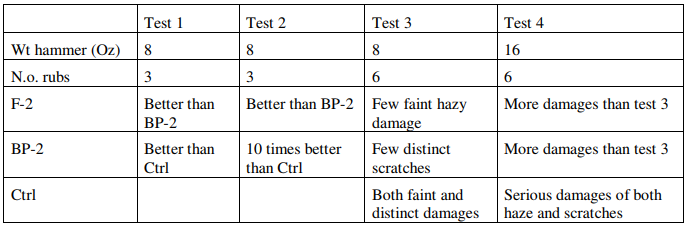
Sample F-2 was tested against wheel abrasion on a Taber Abraser model 503 instrument. Weight
losses were monitored as a measure of abrasive resistance during the course of study, approximately 12 stages of 1000 cycles/stage test. Samples with lower nanoparticle contents were also evaluated as a comparison. Figure 3 showed the result. The sample was almost 2 times better than the counterpart control without nanoparticles. Higher nanoparticle content seems to be needed to get noticeable improvements.
Conclusions
Polyurethane acrylate based UV-curable nanocomposite coatings were prepared and evaluated.
Both surface modified and nonmodified nanoparticles were investigated. Oligomers and monomers with different functionalities were selected to generate nanocomposite samples. Selections were based on the consideration of niche market demand of products with projected specifications, company product portfolio, and facility requirements. Targeted improvement areas included antiabrasiveness, tensile strength, hardness, optical clarity, and dimensional stability, while minimizing adhesion loss and elongation. Results indicated that some systems in this report showed outstanding scratch resistance,antiabrasive resistance, reduced shrinkage loss, and optical clarity. Adhesion did not changesignificantly on substrates Polycarbonate, Polyacrylate, ABS, HDPE, Steel, Aluminum, Stainless Steel,and Glass.
Previous: A Study on Total Heat Loss of Clothing Materials for Firefighters
N e x t : What is seam?