
NewsInformation Center
Why is Scrub Resistance of a Paint Important?
2017/12/22
Paints often become soiled, especially near doorways, windows, and in work and play areas. These test methods cover the determination of the relative resistance of different paints to erosion when repeatedly scrubbed during the life of the paint.
In the paint industry, the property of scrub resistance is measured as the ability to resist wearing or degradation of a dried paint film. The wear or degredation is assessed either visually or by weight loss, when using a scrubability instrument or an abrasion tester.
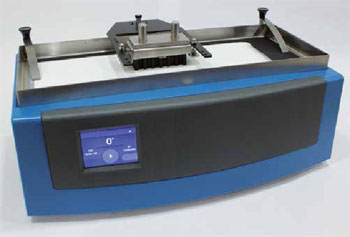
According to the ASTM test methods governing scrub resistance testing, the paint should be formulated to withstand scrubbing with a nylon brush or cloth for a set number of cycles of washing/cleaning when using a nonabrasive or abrasive cleaning media as outlined in the methods, or another cleaner specified by the end user; i.e., common household cleaners.
In the paint industry, the property of scrub resistance is measured as the ability to resist wearing or degradation of a dried paint film. The wear or degredation is assessed either visually or by weight loss, when using a scrubability instrument or an abrasion tester.
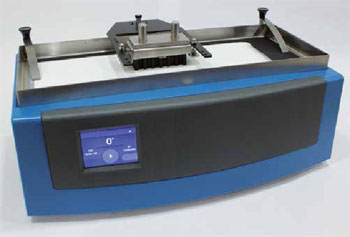
According to the ASTM test methods governing scrub resistance testing, the paint should be formulated to withstand scrubbing with a nylon brush or cloth for a set number of cycles of washing/cleaning when using a nonabrasive or abrasive cleaning media as outlined in the methods, or another cleaner specified by the end user; i.e., common household cleaners.
The paint to be evaluated is applied to a black plastic scrub panel at a required wet film thickness and allowed to dry at laboratory conditions for a pre-determined time, usually 7 days. The thickness of the applied paint may be specified by the coating manufacturer or by the end-user requesting the testing. All parameters for testing, including film thickness, conditions of cure time and duration of cure time are documented with the test results.
The panel containing the dried paint film is placed into the scrub instrument and tested for a pre-determined number of cycles. The number of cycles is selected based on the type of paint or the end-use of the material, or based on a set number of cycles to determine conformance to a maximum weight loss criteria. During testing, the film is observed periodically for visual signs of wear/failure. Failure of a coating film is considered thinning or wear-through along the test path, which is frequently revealed as a change in the color.
If there are no early indications of wear, the testing continues until the agreed upon number of cycles is complete. If the film is to be evaluated for resistance to weight loss, it is tested alongside a calibration (control) panel and the scrubbing action is simultaneous to produce identical wear exposure on each material. The initial and final weights are used to calculate a wear value for the control material and the test material, to provide the end-user with ratio of the wear properties of the two materials.
If there are no early indications of wear, the testing continues until the agreed upon number of cycles is complete. If the film is to be evaluated for resistance to weight loss, it is tested alongside a calibration (control) panel and the scrubbing action is simultaneous to produce identical wear exposure on each material. The initial and final weights are used to calculate a wear value for the control material and the test material, to provide the end-user with ratio of the wear properties of the two materials.
The expectations and the rated results can vary depending on the category of paint and the anticipated use of the material. For example, an exterior gloss should show no visual evidence of gloss reduction, thinning of the dried film or wear-through (wearing of the coating along the test path that reveals 100% of the black panel thru the dried film) after a high number of cycles. In contrast, an interior flat primer may only be required to exhibit no visible wear after a lower number of cycles.
Previous: Glow Wire Test For Electrotechnical Products
N e x t : The Fabric Stiffness Testing Procedure