
NewsInformation Center
Cutting resistance test procedure in ASTM F1790-05
2023/07/03
1. Specimen:
Cut a random sample of 50mm*100mm from any laboratory sampling unit. Cut all woven structures on an inclined plane with the goal of achieving an angle of 45° between the warp and weft directions of the fabric and the blade.
2. Experimental preparation:
2.1 Test setup:
2.1.1 Insert the cutting test device without a heavy object or with the blade in the operating position.
2.1.2 Turn on the machine and adjust the motor-driven balance arm to the ready position.
2.1.3 Calibrate the lever arm balance. See accessories or instrument manufacturer's operating instructions.
2.2 Specimen mounting:
2.2.1 Cover the end face of the mandrel with double-sided adhesive tape.
2.2.2 Place a 6 mm conductive foil strip on the double-sided tape centered on the length of the mandrel. Clamp the end of this foil to the mandrel or securely fasten it to a circuit that is otherwise detected as cut.
2.2.3 Without stretching or twisting the specimen, place the specimen on the tape with the surface to be cut facing upwards. Press firmly on the specimen.
2.2.4 Insert the mandrel into the support column so that the round face faces the motor-driven balance arm and center it so that the blade contact is centered on the round face. If appropriate, tighten the mandrel
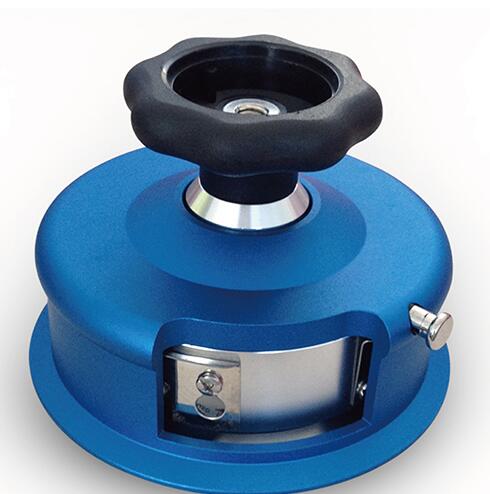
3 Verification of tip supply:
3.1 Calibrate the tip supply using neoprene sheet calibration material.
3.2 Cut a 50mm*100mm sample of calibration material and follow the setup procedure detailed in 2.2.
3.3 At the beginning and end of each sample test, use a 500g load on the calibration material to verify the blade supply, or verify the supply or production lot number of one blade out of every 20. If using the TDM-100 tester or a modified CPP tester, the length of the calibration material across must be between 15 and 25 mm. If using a straight arm CPP tester, the cut length of the calibration material must be between 10 and 15 mm. The cut lengths of all blades should not differ by more than 10 mm. If the cut is within the allowable range, read the distance meter and record the distance.
3.4 When the cut-through line is outside these distances, check the following:
3.4.1 The cutting edge used is new.
3.4.2 The neoprene material is the same as specified.
3.4.3 The calibration procedure for the lever arm indicates that the force at the point of contact is generated by an effective weight of 500 g, allowing for any lever arm effect.
4 Test procedure
4.1 Cut the specimen and install it according to the installation procedure detailed in 2.2.
4.2 Check that the cutting arm is in the ready position. All cuts are made with the blade moving in the same direction.
4.3 Insert the new blade into the arm slot. Keeping it taut and fully secured in the mounting slot, tighten the blade clamping system.
4.4 Ensure that the blade does not touch the test piece
4.5 Select and install the weights.
4.6 Press the zero button on the distance meter
4.7 Carefully bring the blade into contact with the specimen and start the machine immediately. Ensure that only the edge of the blade and not the corner of the blade touches the specimen
4.8 The blade should be cut off within a period of time completely through the blade. This machine will automatically stop. When the cut length is in the range of 5mm ~ 50mm, read the distance meter and record the distance and the corresponding load.
4.9 For conductive materials, take care to avoid premature connection. An 8 mm strip of thin paper may need to be carefully aligned with the top of the conductive foil strip before positioning the sample.
4.10 If the blade does not cut through during the entire cross-cut, stop the machine. Lock the cutting arm to the specimen with the blade and remove the weight and the blade. Move the specimen 6 mm to a new place, install a new blade and return the motor-driven counterbalance arm to the ready position. Increase the load, set the distance meter to zero and retest.
4.11 Lock the blade from the specimen to the cutting arm and remove the weight and blade. Move the specimen 6 mm, install a new blade, increase or decrease the load, return the motor-driven counterbalance arm to the ready position, zero the distance meter, and retest. Continue to test for changes in load until a cut-off is observed in one of the leads, causing the machine to stop. If the cutout is within the acceptable range of 5 to 50 mm, read the distance meter and record the distance and load weight.
4.12 Continue to adjust the load as needed and retest the 5 data points for 5 - 20mm. penetration length range, 5 data points at 33 to 50 mm, and 5 additional points at any load selection between the upper and lower penetration length ranges. For high-strength materials, alternative assignments of the test load of 15 cuts may be considered. Additional tests may be performed at the discretion of the technician.
Previous: Shoe bending tester consists of what structural components
N e x t : What diseases can a respiratory resistance tester be used to detect?