
NewsInformation Center
Talking about the plane abrasion test of textiles
2021/10/18
When a flat object rubs against a flat material, plane wear occurs. Flat resistance is good for most materials because the friction force is distributed over a wide area. However, for many products, when the curve is gradually curved or the curve is shallow, such as when a shirt or jacket is bent across the wearer's back or an upholstered chair seat, flat abrasion resistance will appear (kadolph, 2007). Martindale Wear Tester, Taber Wear Tester, and Uniform Wear Tester are instruments for studying the mechanism of plane wear.
In the Martindale Abrasion Tester, a circular specimen is rubbed against a standard fabric under a known pressure. The wear resistance is measured by frictional movement of the sample in the form of a geometric figure, which represents Lissojous movement, that is, a straight line gradually widens until it forms another straight line in the opposite direction and runs along the Move in a straight line. Another unknown number of pressure and grinding conditions (ASTM D 4966). The advantage of the Martindale abrasion test is that the fabric samples are abraded in all directions. Due to surface friction, the stress develops from the force acting on the fiber axis transversely along the fiber direction; the size of the surface friction generated is directly related to the roughness of the standard worsted fabric abrasive.
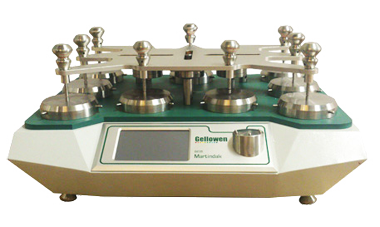
The sample is round with a diameter of 38 mm or 140 mm. Usually, the abrasive is silicon carbide paper or woven worsted wool, whose specifications are shown in Table 2, installed on the felt. The polyurethane foam tray is placed under the sample, and its mass/unit area is less than 500 g/m2. The small sample sits on the large abrasive tool, and then circulates back and forth. If the evaluation of the appearance change requires a test, a larger test piece (140 mm in diameter) is required. The effect is the opposite, placing the abrasive in a holder with a sample-based platform. Apply a force of 9 (for clothing fabrics) or 12 kpa (for interior decoration and technical fabrics) to the top of the sample to resist the abrasive. At the beginning of each test, if the test continues to exceed this value, the standard abrasive should be replaced after 50,000 cycles.
Rotating platform double-head method (Taber grinder) can be used for most fabrics. Under the conditions of controlled pressure and grinding, the sample is ground by rotating friction, and the sample is abraded in multiple directions by rotating friction. The grinding head of the rubber-based composite material simulates mild and severe wear. The specimen mounted on the turntable platform rotates along the vertical axis with the two grinding wheels sliding and rotating. The fabric is subjected to the abrasion action of the two grinding wheels pressed against the rotating sample. The wheels are arranged on completely opposite sides of the sample so that they are rotated in the opposite direction by the rotation of the sample. One friction wheel rubs the specimen outwards, and the other rubs the specimen inwards. The resulting wear marks form a cross-arc pattern on an area of approximately 30 square centimeters. The load can be adjusted by changing the load on the grinding wheel on the specimen (ASTM D 3884).
In ASTM D 4158, a uniform wear tester is used. In this device, the sample is mounted on a support, and wears uniformly in all directions on the plane and every point on the surface of the sample. The uniform wear tester consists of an abrasive installed on the lower end of the shaft, a weight placed on the upper end of the shaft to generate a constant pressure between the abrasive and the sample during the entire test process, and used to raise and lower the abrasive, shaft and weight. Consisting of levers and cams. The surface of the abrasive is basically located on a plane parallel to the surface of the supporting sample, and is pressed against the sample. The abrasive and the sample are rotated in the same direction on a non-coaxial axis parallel to 0.0025 mm (0.0001 in.) at very close but not exactly the same angular velocity (250 rpm). The slight difference in speed is the sample that allows each part to come into contact with a different part of the abrasive each time it rotates. Each rotation is equivalent to one cycle (ASTM D 4158).
Previous: Martindale wear tester test details analysis
N e x t : Mask Synthetic Blood Penetration Tester test process and steps