
NewsInformation Center
What kinds of wear test equipment are commonly used in the world?
2023/02/02
There are four kinds of testing instruments widely used for wear resistance: abrasion tester, scratch tester, oscillation tester and linear abrasion tester. The formulation of coating wear resistance test methods and standards unifies and standardizes the test methods and quality requirements of different materials, and also provides the design basis that must be followed for the development and development of various standard wear resistance test instruments. Next, Xi'an Yanshuo will introduce several common wear tests.
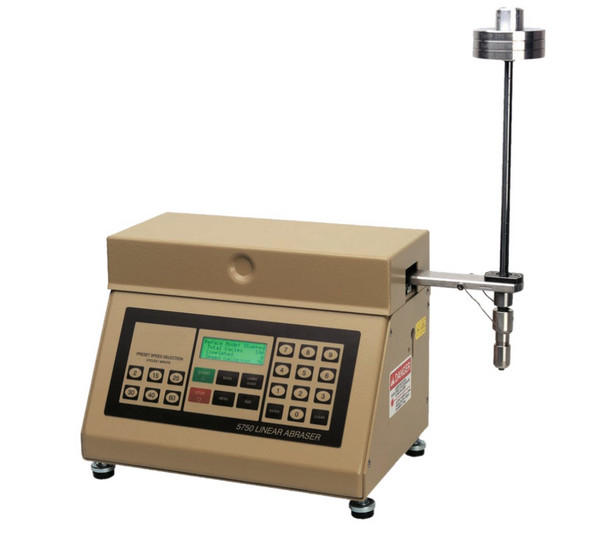
Rotating friction rubber wheel method (Taber test)
Although the working principle of the methods and instruments specified in the Chinese standard GB/T1768-79 (89) is the same, the rotating speed of the rotating disc is not clearly specified, and the test results are only expressed by a single method of coating mass loss (weight loss method) after the specified number of grinding revolutions. The rotary friction rubber wheel method can be widely used for the wear resistance test of coatings, coatings and metal and non-metallic materials, but the rubber wheel used for grinding needs to be frequently trimmed and timely updated. The international standard ISO7784.2-97 stipulates that the abrasion resistance of the coating shall be determined by rotating friction rubber wheel method, that is, under the specified test conditions of rotating disc speed of 60r/min and pressure arm bearing a certain load, the hard rubber wheel embedded with emery abrasive shall be used to abrade the coating surface, Its abrasion resistance can be expressed and evaluated by the average value of the coating mass loss (weight loss method) after the specified number of grinding revolutions or by the average number of grinding revolutions (number of revolutions method) required to wear a certain thickness of coating. Compared with the two methods, the weight-loss method has strict requirements on the weighing accuracy of the sample, but it is not affected by the thickness of the coating; The revolution method is intuitive and convenient, and does not need to be weighed, but it has strict requirements for the measurement of coating grinding thickness.
Test method for abrasion resistance of coatings
Abrasion resistance of coating refers to the ability of the coating surface to resist certain mechanical action, which is usually measured by grinding wheel or sand impact test. It is one of the important characteristics of the coating that is often subject to mechanical wear during use, and is closely related to the hardness, adhesion, flexibility and other physical properties of the coating. Test methods and main technical characteristics of coating wear resistance commonly used in the world.
Falling sand scouring test method
With this test method, the selection of natural sand abrasives will have a direct impact on the test results, so the hardness, particle size and geometric shape of sand particles are strictly required. The Chinese standard GB/T5237.5-2000 stipulates that standard sand conforming to the requirements of GB/T178-77 standard is used as abrasive. ASTMD968-93 stipulates that the abrasivity of organic coatings shall be measured by using the sanding abrasivity tester, that is, natural quartz sand from the specified place of origin shall be used as abrasive, and the surface of the sample shall be washed down freely from a certain height through the test tube, and the volume (L) of abrasive consumed by the unit thickness coating of the specified area shall be abraded, and the abrasivity of the coating shall be evaluated by calculating the abrasivity coefficient. It should be pointed out that in the two standards mentioned above, which adopt the sand drop scouring test method, although the wear resistance tester with the same main technical parameters is adopted, due to the different particle sizes of the natural sand abrasives used, the flow rate of the abrasive with the same outflow volume of 2L is different. The former is defined as 21~23.5s, and the latter is defined as 16~18s.
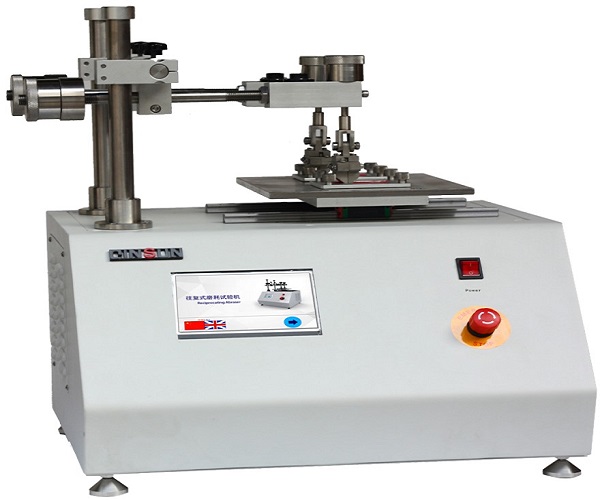
Sandblasting impact test method
ASTMD658-81 (86) stipulates that the abrasion resistance of organic coatings shall be determined by blast abrasion (sand blasting) test. This method is to adjust the output pressure of the air pump to make the air flow rate at the nozzle of the tester be 0.07m3/min, so as to ensure that an average of (44 ± 1) g of corundum beam is sprayed every minute to impact the coating, and the abrasion resistance of the coating is evaluated by calculating its abrasion coefficient based on the mass (g) of the abrasive consumed by the unit thickness coating of the specified area. Therefore, the particle size range of 75~90 must be selected according to the standard μ M silicon carbide is used as abrasive, and the output pressure of air source and the uniform spray speed of abrasive become the decisive factors affecting the test results.
Abrasion test method for reciprocating transportation
After several times of grinding, the coating thickness( μ m) Or the reduction of the coating mass (mg), and the wear resistance of the coating is evaluated by calculating its wear resistance. Both ISO8251-87 and JISH8682 stipulate that the abrasion resistance of aluminum and aluminum alloy anodic oxide film shall be measured by the abrasion wheel abrasion tester. This test method is to make the coated abrasive paper and the abrasive paper bonded on the outer edge of the friction wheel move in a plane reciprocating motion under the specified test conditions, and the friction wheel rotates for a small angle (0.9o) after each double stroke. Because the test conditions of this method are easy to control, there are no other problems that are difficult to control, such as grinding wheel repair, aging, sand flow rate, sand beam shape, etc., in other methods, so the repeatability of the test results is good, Besides coating, this method has been widely used in the abrasion resistance test of plastic, rubber and metal materials.
So far, developed countries have corresponding wear test methods for different materials. For example, the Japanese industrial standard JISH8503 specifies the test methods for the wear resistance of metal film; JISH8615 describes the abrasion resistance test of chromium electrodeposit; For example, the American Society for Testing and Materials standards ASTMD968-93 and ASTMD658-81 (86) stipulate that the sand drop method and sand blasting method are used to determine the abrasion resistance of organic coatings; In the international standard SO7784.2-97, the abrasion resistance of paints and varnishes is determined by rotating friction rubber wheel method; It is specified in IS08251-87 and JISH8682 that the wear resistance coefficient of anodic oxide film on the surface of aluminum and aluminum alloy shall be measured by the friction wheel wear tester.
Previous: What should be paid attention to when purchasing a fatigue testing machine?
N e x t : Operation steps of automobile interior material flammability tester